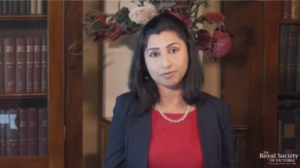
‘We can find all the answers when we dig further into nature,’ says Nisa Salim. ‘The potential to use nature as a template for developing new technologies is exciting.’
She creates multifunctional materials inspired by nature to solve challenging problems.
The Royal Society of Victoria is delighted to congratulate Dr Nisa Salim, Swinburne University of Technology Vice-Chancellor’s Initiative Research Fellow, the 2020 recipient of the Phillip Law Postdoctoral Award for the Physical Sciences.Nisa’s work in carbon fibre manufacturing is driven by the need to develop greener, safer, and more sustainable transport systems. The transport sector accounts for 18% of all greenhouse gas emissions in Australia, growing faster in this sector than in any other.Nature holds the key to many problems, such as water management, climate control, high speed travel, etc. The design of Japanese bullet trains, for example, is based on the beak of kingfisher birds that dive at high speeds from air to water with little splash. In addition, the microgroove structure of sharks’ scaly skin is used to innovate aircraft wings, wind turbine blades and Olympic swimsuits as it allows for streamlined movement. Robots have also been designed to mimic water strider insects to jump on water.‘Everything you see around you is made of materials…they play a significant role in the world, both in the future and now,’ Nisa says. She uses chemistry and engineering to adopt these natural designs into materials at the nanoscale level to make them better than ever.
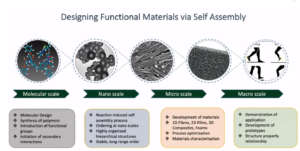
Using a novel molecular self-assembly approach, Nisa develops materials in various length scales and dimensions. Self-assembly is common in nature, and she takes inspiration from the formation of snowflake: without a blueprint to direct them, billions of water molecules arrange themselves into a unique snowflake.Nisa designs and synthesises polymer molecules and direct them to self-assemble. Self-assembly is regarded a “bottom-up” manufacturing approach as the final structural is encoded in the shape and properties of the molecules used, compared to traditional techniques which carve out structures from a larger block of matter (e.g., a tunnel formed by placing bricks into a cylindrical shape as opposed to drilling a hole in rock).
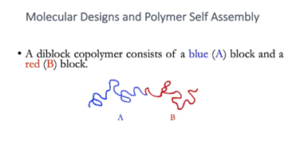
One technique that has attracted significant attention recently is block copolymer self-assembly. Block copolymers consist of two blocks with chemically distinct properties joint by a covalent bond. For example, hydrophilic and hydrophobic molecules that are water-loving and water-hating respectively can be joined so that they cannot be separated. Water and oil visibly separate when mixed together, however, as copolymers, on the nano-level they will self-assembly into shapes such that the hydrophobic components huddle together to hide from water, such as micelles or vesicles.
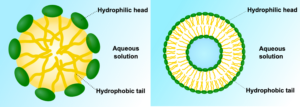
Left: Micelles - Hydrophobic tails face inwards and the hydrophilic component acts as a barrier from the water. Right: Vesicles – a lipid bilayer (two layers of lipid molecules) arranged such that all hydrophobic tails are directed into the centre of the membrane, away from water. An aqueous hollow is formed in the centre.
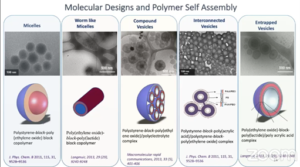
These spherical particles can be used as nano-carriers, encapsulating things such as drugs and other compounds. They show great promise for targeted drug delivery applications to release drugs in specific tissues. Nisa creates spherical micelles, worm-like micelles, compound vesicles (smaller vesicles within a larger one), interconnected vesicle channels.Particles can then be shaped into nanostructures that are completely different to the individual molecules. Different shapes can have different useful properties and applications. For example, hexagonal structures inspired by honeycomb can be used to produce solar cells to create electricity from light, and lamellar structures are useful in electrical transistors.Nisa introduces attractive and repulsive forces to make molecules interact, forming nano-scale structures, which are then used to form microscale materials, and then finally macroscale devices and structures that we can use. By carefully choosing the polymer blocks and components, changing their chain length and molecular weight, she can create fabricate various nanostructures in solution and solid states.‘When we embrace the mimicking of nature, we can make amazing structures and innovations,’ Nisa says. ‘We still haven’t explored nature very well...I’m still learning.’Following a nearly two-year career break, Nisa moved into a completely new field when she returned to research: carbon fibre.
Nisa joined Deakin’s carbon fibre research facility, Carbon Nexus, as an Associate Research Fellow in 2014.These synthetic hair-like fibres are ten times thinner than human hair and lighter than aluminium yet eight times stronger than steel. They therefore have enormous potential in transport and building construction as they can maintain the same or greater strength while reducing weight.Porous carbon fibres can be used to create structural supercapacitors and batteries that can store electrical energy in lightweight components of cars, aircrafts or drones. This way, the battery is integrated into the structural components rather than vehicles requiring additional heavy, sole-purpose batteries.To further extend her work, Nisa was supported by two fellowships to visit aerospace and automotive giants and the world’s leaders in ‘wet spinning’ carbon fibre technology. Wet spinning is a process that spins fluid polymers in a chemical bath that causes the fibre to precipitate and solidify as it emerges.
Nisa was awarded an Endeavour Fellowship to visit the University of Kentucky, which had a unique wet spinning method of creating carbon fibre. She then visited automotive and aerospace industries in the USA to gain an understanding of industry requirements on low cost, high strength carbon fibres.Leveraging her collaborative relationships with a global academic and industrial network, Nisa has propelled this cutting-edge research from the lab to the commercial market.After a second career break, Nisa began building on her fibre carbon work to manufacture 3D porous multifunctional materials. She and her research team work with global collaborators and Australian small to medium enterprises to explore the potential applications of these new materials. If structural components of vehicles could also be the power supply, drones could be built to carry heavy loads with a long battery life to deliver supplies to those who are affected and isolated during flood, bushfire, or pandemics.In a project in collaboration with CSIRO, Nisa is refashioning our waste into carbon fibre materials. We waste 7.3 million tonnes of food – the equivalent of 300 kg per person per year and 5% of Australia’s greenhouse gas emissions. The goal of this project is to extract collagen from animal tissues (e.g., bone, skin, uneaten parts, etc.), to make porous carbon fibre-based materials.Stronger than steel, lighter than aluminium and electrically conductive, the porous carbon fibres that Nisa creates are essential multifunctional materials for the future of sustainable and smart transport systems.
Taking inspiration from nature for the structural design, Nisa hopes to give back to nature as we create better and more sustainable vehicles.
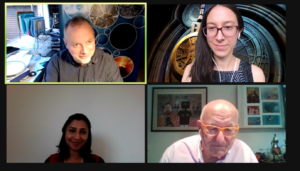
This article was written by Catriona Nguyen-Robertson and details the online presentation given by the 2020 Phillip Law Postdoctoral Award for the Physical Sciences recipient, Dr Nisa Salim, on 26th Nov 2020.
Discover how you can join the society
Join The Royal Society of Victoria. From expert panels to unique events, we're your go-to for scientific engagement. Let's create something amazing.
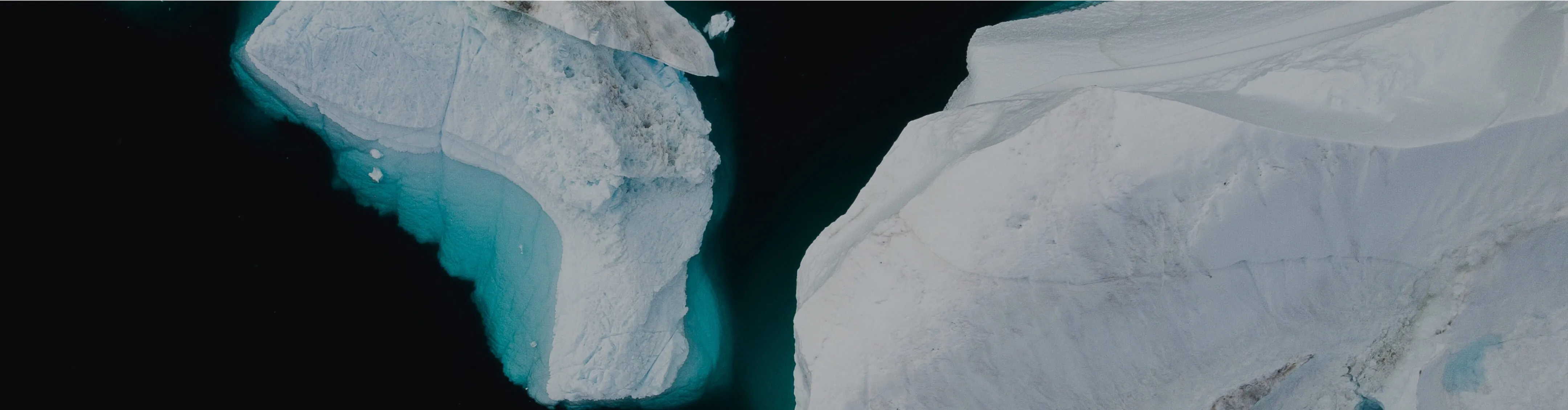