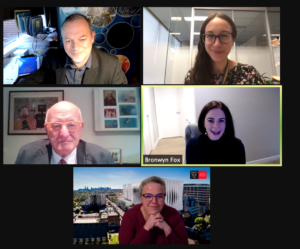
L-R top-down: Mike Flattley (RSV CEO), Catriona Nguyen-Robertson (RSV Science Communications Officer), David Zerman (RSV President), Prof. Bronwyn Fox (RSV Medal for Excellence in Scientific Research Recipient and Deputy Vice-Chancellor (Research and Enterprise) at Swinburne University of Technology), Prof. Sally McArthur (Director, Manufacturing Futures Research Institute at Swinburne University of Technology)[/caption]The Royal Society of Victoria is delighted to congratulate Professor Bronwyn Fox as the 2020 recipient of the Medal for Excellence in Scientific Research.Bronwyn is dedicated to driving excellence in research, innovation and leadership. She has driven the growth and development of Australia’s advanced manufacturing ecosystem, and because of her efforts, was appointed Deputy Vice-Chancellor (Research and Enterprise) at Swinburne University of Technology.“[She] exemplifies the goal of bringing science and industry together in Victoria, and to establish Victoria as an international science capital,” says RSV Councillor, Dr Catherine de Burgh-Day.Brownyn’s mission is to support the transition of Australia’s manufacturing sector to the fourth industrial revolution.[caption id="attachment_7052" align="alignright" width="300"]
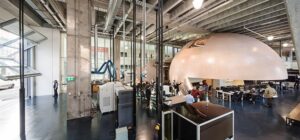
Advanced Manufacturing Industry 4.0 Hub (taken from Swinburne University of Tech’s website)[/caption]‘Industry 4.0 offers enormous opportunities for Australian manufacturers,’ says Bronwyn. ‘We can re-shore manufacturing in a highly competitive way, especially by translating learnings from our world-leading mining sector into other manufacturing processes. We will be able to produce high value, low-cost components here in Australia.’There have been four industrial revolutions over the past four centuries. The first was mechanisation in the 18th century, led by steam power. Then electricity and oil-based power supported mass production. A new era of computers and electronics drove automation. And now, building on the previous three revolutions, new technologies are emerging for digitalisation that provide the capacity for smarter, self-correcting manufacturing processes.[caption id="attachment_7053" align="alignleft" width="300"]
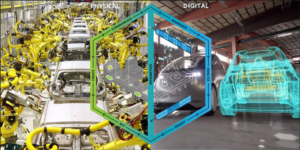
Digitalisation of manufacturing processes by using “digital twins” to simulate processes and physical objects.[/caption]Bronwyn is fascinated by carbon and carbon fibre materials. Changing the arrangement and bonding between individual carbon atoms can achieve very different outcomes. Carbon can form the hardest known material – diamond – or become graphite lubricant. Carbon fibre composites have been around since the 1970s and are are becoming increasingly adopted by industry. They have so far been used in aerospace and automotive applications to produce strong, lightweight structures that reduce environmental emissions and improve fuel efficiency as the load is lighter. For example, the Boeing 787 Dreamliner is comprised of 50% composite material, saving around 20% in fuel, and BMW is using carbon fibre composites to produce lightweight electric cars so that the battery can take the car further.By splitting the layers of graphite apart into single layers of latticed carbon atoms, a new material, graphene, was discovered. Graphene could radically change the manufacturing and infrastructure industries, especially once it becomes price competitive. Current research is exploring its use in enabling 6G communications, photovoltaics (solar cells), energy storage, and creating smart sensing materials (e.g. detecting leaks of hazardous materials in the environment).But we are only at the beginning of its industrial applications. Bronwyn is spearheading work to ensure its quality and ease of production.[caption id="attachment_7054" align="alignright" width="269"]
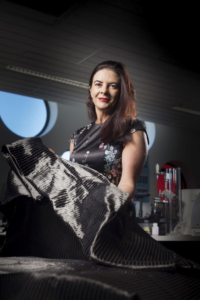
Bronwyn with a carbon fibre composite material[/caption]Bronwyn’s journey in carbon fibre composites began during her PhD in Engineering at the Australian National University. At the time, advanced polymer composites showed enormous potential as they were extremely strong and light – around 10 times the strength to weight ratio of most metals. But they were out of reach of most manufacturers as they were expensive and time-consuming to make. Bronwyn worked with Dr Jonathan Hodgkin at CSIRO to fabricate these materials faster and cheaper while retaining a high quality suitable for aerospace applications.She then continued this work when she joined Deakin University and became involved with a new rapid cure process from a small start-up called Quickstep. Carbon fibre composite material was originally formed in an autoclave (vacuum pressure oven) in a highly energy inefficient process – and it was Bronwyn’s hatred of the machine that drove her to reform the method. Nearly two decades later, Quickstep are now Australia’s largest independent manufacturer of composite materials and exporting aerospace components in the global market, and the production time of a single component has been reduced from 20 hours to one minute.In 2006, Bronwyn’s relationship with CSIRO and Quickstep led to her taking a sabbatical at the University of Manchester, the home of Graphene. This seeded the inspiration to create a research facility in Australia focused on the manufacture of the raw materials that comprise carbon fibre composites. She knew that there was a demand for carbon fibre production but no mechanism with which to supply that demand.Bronwyn was one of the founders of the Carbon Nexus facility at Deakin University, together with former CEO of VCAMM and Chief Engineer at Holden Special Vehicles, Professor Brad Dunstan. The innovation hub created a Composites Manufacturing Ecosystem that brings together multidisciplinary teams and industry-research partnerships, contributes to national manufacturing capability, supplies products and services globally, and provides around 1,400 jobs in the Geelong region.To further improve the manufacturing process, Bronwyn wanted to gain better control of carbon fibre composite chemistry. In addition, while traditionally made from crude oil, renewable carbon fibres are also coming onto the scene (e.g., biobased acrylonitrile made from sugars). Brownyn and her colleagues put a case forward to CSIRO to collaborate in the manufacturing of polyacrylonitrile (PAN), using their unique, raft polymerisation technology, which provides greater control at the molecular level. Dr Cathy Foley, CSIRO Chief Scientist, replied to the pitch: ‘This is great! How do I push the “go” button?’ Those words of encouragement made all the difference to the project. A trade-off with greater molecular control, however, is defects in the fibre making. With a focus on the chemistry, foreign particles and air bubbles started to creep into the fibres. By removing these, the fibres can become much stronger. A breakthrough by researchers at the University of Bayreuth last year showed that forming fibres by electrospinning and then crosslinking them, they could form an incredibly strong and tough rope fibre – originally fibres were either strong or tough, but not both. Bronwyn hopes that molecular control from the CSIRO technology can be combined with the electrospinning yarn approach to form materials that are better than ever.At the beginning of the year, Bronwyn led the establishment of the National Industry 4.0 Testlab, the world’s first industrial scale 3D printing approach to making carbon fibre composites. By building from the bottom up, layer by layer, it becomes possible to create smarter materials that are light weight have reduced manufacturing cost and waste generation. Integrating sensors into the materials at they are being built means that we can create cars and other products can tell us when they need repair.[caption id="attachment_7051" align="alignleft" width="446"]
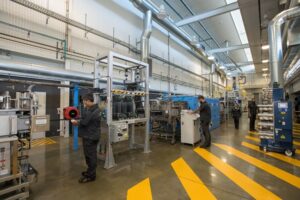
Deakin Carbon Nexus (taken from their website)[/caption]Brownyn is also leading a collaborative proposal for an Aerostructures Research Innovation (AIR) Hub to undertake innovative R&D in the emerging aerospace sector in Victoria. It will leverage facilities, such as those she has taken a lead in establishing (Carbon Nexus and the National Industry 4.0 Testlab), to create advanced composite structures for automotive, surface transportation and civil construction applications.Instead of spending $10,000 to launch each kilogram of a rocket into space, rockets could become more light weight. Unmanned aerial vehicles (drones) could be used to assist natural disasters and delivering supplied to remote places that can travel further than before. Vertical take-off and landing vehicles may be the future of an “Uber flight” concept of transportation. Bronwyn sees Victoria at the heart of these exciting developments and wants to see people on board to create a local supply chain.‘I am a strong believer that people are at the heart of technology, and that technology is at the heart of scalable societal change and benefit,’ she says.Bronwyn has endeavoured to join industry and academia to propel Australia’s manufacturing processes so that we could be the world leaders of advance composite material manufacturing. ‘I love putting industrial-level equipment on university campuses,’ she says. Her efforts have been instrumental in placing Australia at the forefront of the fourth industrial revolution.
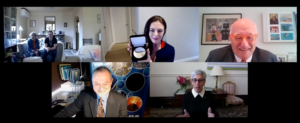
This article was prepared by Catriona Nguyen-Robertson and details the online presentation given by Royal Society of Victoria's Medal for Excellence in Scientific Research recipient, Professor Bronwyn Fox, on 10th Dec 2020.
Discover how you can join the society
Join The Royal Society of Victoria. From expert panels to unique events, we're your go-to for scientific engagement. Let's create something amazing.
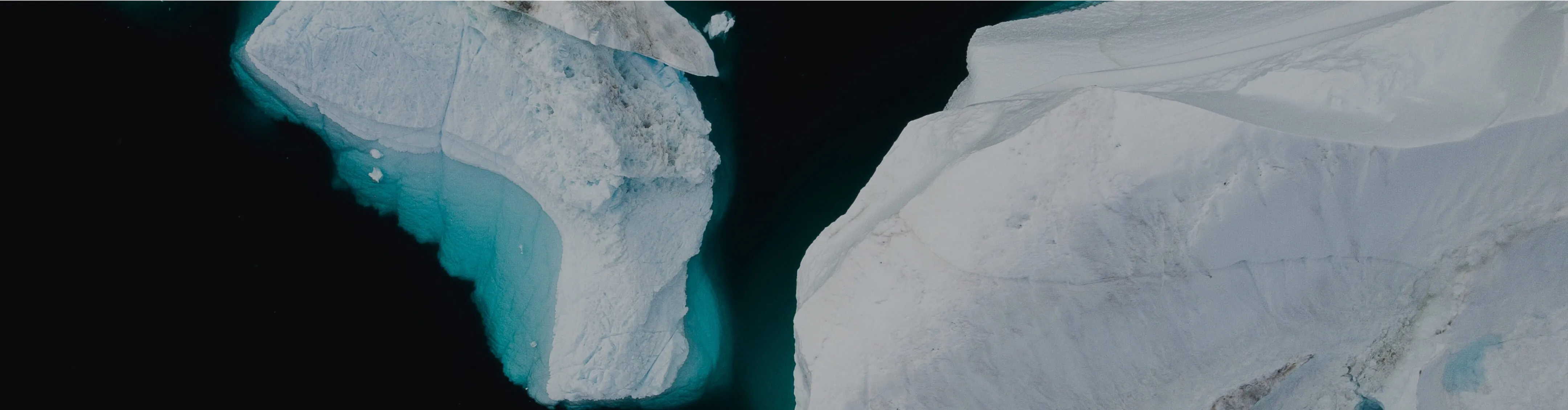